摘要:燃煤電廠選擇性催化還原(SCR)脫硝系統(tǒng)氨逃逸問題普遍存在,為良好控制逃逸氨濃度,采用靛酚藍分光光度法在現(xiàn)場對煙氣中氨濃度進行了測試。以內(nèi)蒙古某200MW級燃煤機組氨逃逸性能試驗為例,詳述了靛酚藍分光光度法現(xiàn)場測試的操作方法與流程,并將試驗結(jié)果與現(xiàn)場在線儀表數(shù)據(jù)進行了比較,同時分析了煙氣中飛灰對該方法測試結(jié)果的影響。結(jié)果表明,現(xiàn)場測試可獲得不同取樣點逃逸氨的濃度,對噴氨控制有利;樣品中灰分的存在會大幅提升吸光度值,使測試結(jié)果偏高,采樣過程中需嚴防灰分進入樣品,以便獲得正確的分析結(jié)果。
0引言
過量的氨逃逸會給電廠帶來一系列風險,準確監(jiān)控逃逸氨濃度以控制噴氨量,對電廠的安全與經(jīng)濟運行至關(guān)重要。
目前,電廠檢測煙氣中氨濃度的方法主要有激光原位法和抽取采樣法。其中,激光原位法往往受粉塵和振動等現(xiàn)場條件制約,在測量時存在較大偏差,且易出現(xiàn)跳變現(xiàn)象。實際逃逸氨濃度多依靠定期的手工測試進行檢驗修正,即通過現(xiàn)場多點抽取采樣,樣品在實驗室條件下進行分析。實驗室分析方法有靛酚藍分光光度法和離子色譜法等。不同的方法在時效性、準確性及抗干擾性方面存在一定的差異。
本文以內(nèi)蒙古某電廠逃逸氨測試為基礎(chǔ),闡述靛酚藍分光光度法現(xiàn)場取樣及試驗室分析具體的操作流程與方法,并與現(xiàn)場表盤在線數(shù)據(jù)進行比對;受限于現(xiàn)場條件,將粉塵對測試結(jié)果的影響考慮其中,探索了樣品中灰分對靛酚藍分光光度法的影響,為后續(xù)現(xiàn)場逃逸氨測試提供依據(jù)。
1內(nèi)蒙古某電廠脫硝設備現(xiàn)狀
內(nèi)蒙古某燃煤電廠某機組裝機容量為200MW,布置2臺SCR反應器,每臺反應器初裝2層催化劑,1層備用。SCR脫硝裝置設計入口NOx質(zhì)量濃度450mg/m3(標準狀態(tài),下文與體積相關(guān)的數(shù)值均已換算至標準狀態(tài));設計脫硝效率不低于80%,逃逸氨體積分數(shù)小于3x10-6;采用液氨制備脫硝還原劑。對脫硝系統(tǒng)逃逸氨進行現(xiàn)場采樣,并用靛酚藍分光光度法測算逃逸氨濃度。
2材料與方法
2.1測試原理
煙氣中的氨預先被裝有0.05mol/L稀硫酸的吸收液吸收固定生成硫酸銨。在水楊酸稀硫酸的、亞硝基鐵氰化鈉和次氯酸鈉溶液的共同作用下,硫酸銨中的銨離子會發(fā)生顯色反應,生成藍色絡合物,而顯色的深淺與氨離子濃度呈線性相關(guān),利用分光光度計可測算出原始樣品氨濃度。
2.2樣品采集
逃逸氨采集裝置如圖1所示,其由煙氣采集管和吸收裝置等組成。
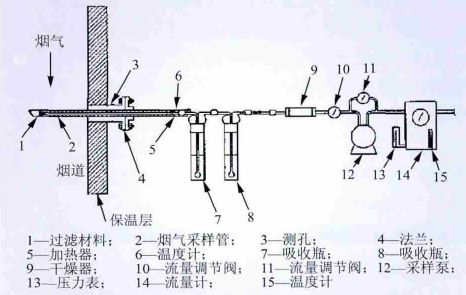
圖1采集裝置示意
采用網(wǎng)格布點法進行試驗測孔采樣,調(diào)節(jié)抽氣流量為6L/min,使鼓泡均勻,采樣時間設定為30min?;瘜W分析所用試劑僅氯化銨為優(yōu)級純,其余均為分析純。所有試驗重復3次,以保證數(shù)據(jù)的可靠性。
2.3試劑配制與樣品測試
試驗所需試劑及濃度如表1所示。
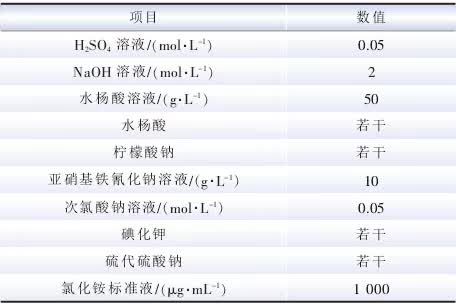
表1試驗所需試劑
采用紫外分光光度計對氯化銨標準液和樣品進行測試,試驗前需預先繪制氯化銨標準曲線。
(1)標樣配制。取7支20mL具塞比色管,分別加入質(zhì)量濃度為10μg/mL的氯化銨標準液0、0.5、1.0、1.5、2.0、2.5、3mL,用去離子水稀釋至10mL,再向這7支比色管中分別加入水楊酸、亞硝基鐵氰化鈉和次氯酸鈉溶液各1.0mL后振蕩,靜置60min待測。
(2)樣品制備。將樣品預先用與吸收液同濃度的稀硫酸定容至250mL,取其中10mL按標樣所列順序加入水楊酸、亞硝基鐵氰化鈉和次氯酸鈉溶液各1.0mL后振蕩,同樣靜置60min待測。
(3)測試。標樣與試驗樣品均在波長為697.5nm處進行吸光度測試。
2.4逃逸氨濃度計算
逃逸氨濃度計算方法為

式中:
為逃逸氨質(zhì)量濃度,mg/m3;A和A0分別為樣品溶液(煙氣吸收液經(jīng)稀釋定容后得到)與空白溶液吸光度;a和b分別為標準曲線截距和斜率;Vs為煙氣吸收液稀釋定容后的總體積,mL(本文為250mL);V0為進行吸光度試驗時從Vs中所取體積,mL(本文為10mL);Vnd為所采煙氣樣品標準體積,L。
為便于測試結(jié)果與電廠儀表數(shù)據(jù)的比對,試驗所測逃逸氨濃度按10-6計量給出,其轉(zhuǎn)化系數(shù)為22.4/17。
3結(jié)果與討論
3.1氯化銨標準曲線
氯化銨標準液吸光度標準曲線如圖2所示。圖2標準液氯化銨含量對應吸光度存在以下關(guān)系:
y=0.054x-0.037
其中相關(guān)系數(shù)平方R2=0.994,接近1,擬合度較高,表明氯化銨濃度與吸光度具有良好的線性相關(guān)性,故可根據(jù)樣品吸光度反推樣品氨濃度。圖中氯化銨質(zhì)量是指25mL測試液中所含氯化銨質(zhì)量。
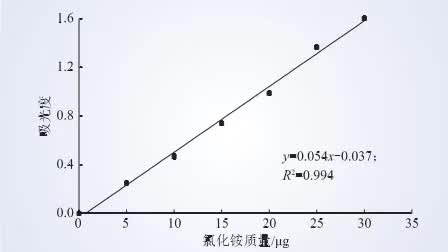
圖2氯化按吸光度標準曲線
3.2逃逸氨樣品測試
采用靛酚藍分光光度法對煙氣樣品進行分析,并將測試結(jié)果與電廠表盤在線數(shù)據(jù)(激光直接測量法,取測試時間段平均值)進行對比,結(jié)果如表2所示。
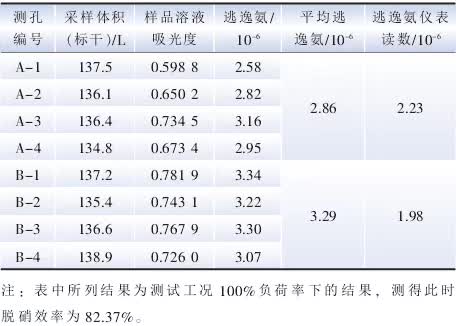
表2逃逸氨測試結(jié)果
由表2可以看出,靛酚藍分光光度法能有效測算出現(xiàn)場氨逃逸數(shù)據(jù).逃逸氨體積分數(shù)在2.5x10-6-3.4x10-6之間,其中部分測點逃逸氨體積分數(shù)超出3x10-6的設計值,可能由于噴氨不均勻或流場分布不均勻所致,此時脫硝效率為82.37%,同樣高于設計值80%的要求。同時發(fā)現(xiàn)所測逃逸氨數(shù)據(jù)要大于電廠儀表表盤顯示數(shù)值,且儀表未檢測出部分氨逃逸超標點狀況。儀表顯示數(shù)值過低可能是儀表由于取樣位置固定,不能全面反映電廠實際氨逃逸狀況;且在線數(shù)據(jù)受粉塵影響,存在較大系統(tǒng)偏差,需要進一步矯正。試驗結(jié)果表明,現(xiàn)場人工測試結(jié)果可為電廠噴氨量調(diào)整及逃逸氨在線測試系統(tǒng)校驗提供參考。
3.3灰分影響分析
盡管網(wǎng)格布點取樣分析法能較為全面地反映電廠氨逃逸狀況,但實際取樣過程中若操作不當會使少量粉塵顆?;烊霕右褐校淇赡軙y試結(jié)果產(chǎn)生影響。為判斷灰分的摻入對靛酚藍分光光度法測試結(jié)果的影響,分別在標準氯化銨樣品(濃度為1μg/mL,體積為10mL)中添加0.01、0.02、0.04g的飛灰,以模擬粉塵進入測試樣品中的狀況。將加入粉煤灰后的各樣品搖勻,震蕩后靜止10min取上清液進行分光光度分析,結(jié)果如圖3所示。
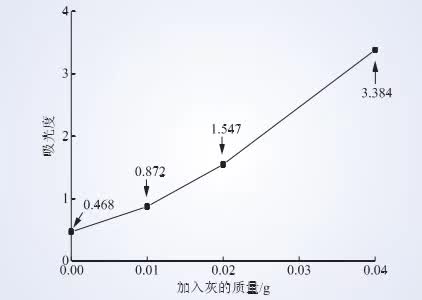
圖3灰分對吸光度的影響
由圖3可見,灰分的加入極大地提升了樣品的吸光度,且初始摻入的灰分越多,濾灰后樣品的吸光度越大,這可能是因為灰中各種可溶性金屬離子及不溶物對測試結(jié)果產(chǎn)生了干擾。文獻認為,采用靛酚藍分光光度法,飛灰(也即本文所描述的灰分)的加入會使樣品引入新的Fe3+、Cu2+、Ca2+和Mg2+等離子,其中Fe3+能明顯增加樣品的著色深度,也即增加吸光值,從而使結(jié)果偏高。文獻則認為,煙氣中的飛灰會吸附一定量自由態(tài)或化合態(tài)的氨,而灰分的摻入使樣品中氨濃度升高,使測試結(jié)果偏大;由于飛灰的吸附作用,會使氨逃逸測試環(huán)境出現(xiàn)系統(tǒng)偏差,建議進行飛灰中氨含量測試方法的研究。對比發(fā)現(xiàn),文獻的測試結(jié)果顯示,其在初始氨質(zhì)量濃度為0.792μg/mL的氨標準液中加入0.02g灰,靛酚藍分析法測出氨濃度的相對偏差只有16.79%,而本文測試條件與文獻相近情況下,灰分對測試結(jié)果造成的影響卻超過了200%。造成這一現(xiàn)象的可能原因是,本試驗只對加灰樣品進行了靜置,未做進一步分離,使少量灰分仍殘留在樣品中。部分殘余的灰分會降低樣品的透光率,導致吸光度大大增加,使結(jié)果偏高。由此可見,要想獲得準確的測試結(jié)果,取樣時嚴格控制飛灰進入樣品非常重要。
4結(jié)語
本文研究結(jié)果表明:現(xiàn)場多點取樣,在實驗室條件下采用靛酚藍分光光度法測試煙氣中的氨,能較好地還原現(xiàn)場氨逃逸狀況,即可較為準確地檢測出部分氨逃逸超標位置,因而可為現(xiàn)場噴氨量控制和調(diào)整提供方位,這一點優(yōu)于現(xiàn)場儀表的在線監(jiān)測;同時,測試結(jié)果也可為儀表示值的修正提供參考。但是靛酚藍分光光度法對灰分的抗干擾性能較差,少量灰分的混入即會對結(jié)果產(chǎn)生極大影響,建議后續(xù)實測過程注重對煙氣吸收液中灰分的濾除。
來源:《中國電力》 作者:李允超等
特此聲明:
1. 本網(wǎng)轉(zhuǎn)載并注明自其他來源的作品,目的在于傳遞更多信息,并不代表本網(wǎng)贊同其觀點。
2. 請文章來源方確保投稿文章內(nèi)容及其附屬圖片無版權(quán)爭議問題,如發(fā)生涉及內(nèi)容、版權(quán)等問題,文章來源方自負相關(guān)法律責任。
3. 如涉及作品內(nèi)容、版權(quán)等問題,請在作品發(fā)表之日內(nèi)起一周內(nèi)與本網(wǎng)聯(lián)系,否則視為放棄相關(guān)權(quán)益。