1 背景
在石油化工生產(chǎn)過程中,常采用NaOH溶液吸收H2S堿洗油品和裂解氣,產(chǎn)生了含有大量污染物的廢堿液。該廢水的特點(diǎn)是生化需氧量(COD)高達(dá)30萬mg/L,同時(shí)含有高濃度的硫化物、酚類、石油類等有毒有害污染物,其pH值在12以上。廢堿液具有難聞的惡臭氣味,強(qiáng)堿性,且含有較高濃度的硫化物和有機(jī)物,若不經(jīng)適當(dāng)?shù)念A(yù)處理,高濃度的廢堿液進(jìn)入污水生化處理系統(tǒng)后,會(huì)抑制微生物的生長(zhǎng)繁殖,嚴(yán)重時(shí)可使微生物大量死亡,從而影響污水處理場(chǎng)的正常運(yùn)行和總排廢水的達(dá)標(biāo)排放。
因石油資源的有限,近年來,甲醇制烯烴行業(yè)迅猛發(fā)展。烯烴分離單元主要采用的是32%的NaOH溶液對(duì)反應(yīng)氣體進(jìn)行洗滌,去除CO2等酸性氣體。在堿洗過程中,會(huì)產(chǎn)生較少量的乳化油、浮油以及烴類聚合物等。為避免烴類聚合物在堿液處理循環(huán)系統(tǒng)中造成相關(guān)的傷害,引發(fā)循環(huán)系統(tǒng)堵塞等,在處理技術(shù)過程中,當(dāng)堿液達(dá)到了堿洗塔底之時(shí),就需要立刻排出,此過程則會(huì)產(chǎn)生出大量的廢堿液。在廢堿液當(dāng)中,含有大量的NaOH、Na2CO3等無機(jī)鹽,呈強(qiáng)堿性,同時(shí),在廢堿液當(dāng)中還含有苯、二甲苯、酚等有機(jī)物質(zhì)。排放之后會(huì)對(duì)環(huán)境造成較大地污染和損壞。因此,廢堿液的治理一直是困擾我國(guó)煉油廠和乙烯廠水污染治理的一個(gè)核心問題。隨著高硫原油加工量的增加和煤制烯烴裝置規(guī)模地不斷增大,廢堿液的排放量也隨之增加,對(duì)廢堿液的治理問題引起了研究人員的重視。
2 廢堿液處理技術(shù)進(jìn)展
2.1 中和法:中和法是指向廢堿液中投加酸性物質(zhì),將廢水的pH值調(diào)至要求的范圍。廢堿液主要采用無機(jī)酸(常用硫酸)和酸性氣體(CO2、H2S)中和,產(chǎn)生的H2S氣體送入火炬燃燒,經(jīng)中和處理后的廢堿液限流排入污水處理廠,經(jīng)污水處理后達(dá)標(biāo)排放。用硫酸中和存在嚴(yán)重的腐蝕問題。由于廢堿液中的組成波動(dòng)較大,給硫酸加入量的控制帶來困難。酸不是過量,就是不夠,從而使得設(shè)備和管線常處于酸堿交替腐蝕狀態(tài)。
2.2 焚燒法:焚燒法是在高溫(≤950℃)和常壓下使硫化物氧化生成硫酸鹽,有機(jī)碳?xì)浠衔锷蒀O2 和H2O,NaOH轉(zhuǎn)化成Na2CO3,硫酸鹽和碳酸鹽仍溶解在處理過的廢液中。在廢堿液的處理系統(tǒng)當(dāng)中,焚燒法的裝置主要是由尾氣凈化設(shè)備、焚燒設(shè)備、前處理設(shè)備、應(yīng)急處理系統(tǒng)等共同組成。焚燒是一種可靠的氧化處理法,操作簡(jiǎn)單,可滿足達(dá)標(biāo)排放要求。缺點(diǎn)是能耗大,操作成本高,其投資成本與簡(jiǎn)單的濕式氧化裝置相仿。且燒嘴因聚合物生成造成結(jié)垢致使廢堿噴射器/霧化器堵塞仍是一個(gè)有待解決的問題。另外,燃料價(jià)格對(duì)選擇現(xiàn)有的焚燒工藝具有很大影響。焚燒法在燃料便宜的地方可以選擇使用。
2.3 濕式空氣氧化法:濕式空氣氧化法(簡(jiǎn)稱WAO)是在高溫(150℃~350℃)和高壓(0.5~20.0MPa)條件下,以空氣中的O2為氧化劑,在液相中將有機(jī)污染物氧化為CO2和H2O等無機(jī)物或小分子有機(jī)物的化學(xué)過程。該法的優(yōu)點(diǎn)是沒有尾氣造成大氣污染問題,但由于需要在較高壓力和較高溫度條件下運(yùn)行,對(duì)設(shè)備要求高,投資較大,能耗高,因此應(yīng)用較少。
2.4 生物處理法:生物處理法是通過微生物的新陳代謝作用,使廢水中的有機(jī)物等污染物質(zhì)被微生物降解并轉(zhuǎn)化為無害物質(zhì)的過程。石油化工廢堿液是一種含高濃度的硫化物和酚類等污染物的有機(jī)廢水。由于高濃度的硫化物和酚類污染物對(duì)常規(guī)生化處理系統(tǒng)微生物有毒害作用,造成常規(guī)生化處理難度大。因此,必須采用適宜工藝對(duì)其進(jìn)行預(yù)處理,以消除硫化物和酚類污染物對(duì)常規(guī)微生物地抑制作用。
3 某煤制烯烴項(xiàng)目情況簡(jiǎn)要說明
某煤制烯烴項(xiàng)目烯烴分離裝置采用Lummus 前脫丙烷后加氫、丙烷洗工藝技術(shù)。烯烴分離裝置在裂解氣壓縮機(jī)二段和三段之間設(shè)有堿洗塔,產(chǎn)品氣進(jìn)入堿洗塔的底部,為了使產(chǎn)品氣和堿液充分接觸,將堿洗塔設(shè)計(jì)為3個(gè)堿洗循環(huán)段,從下到上依次為弱堿段、中堿段和強(qiáng)堿段,堿洗塔能夠脫除裂解氣中的酸性物質(zhì)。在強(qiáng)、中、弱堿段各設(shè)液體收集室,以保證各堿段循環(huán)泵的正常運(yùn)行。塔釜弱堿段用隔板隔為2個(gè)室。
流入大室的液體為弱堿循環(huán)泵提供吸入液體;濃縮油通過隔板溢流到小室,這一側(cè)含油的堿通過液位控制從堿洗塔塔釜靠自壓排到廢堿罐,從而產(chǎn)生含堿廢水。該股含堿廢水曾使用汽槽車將其運(yùn)至廢渣廠處理,存在很大的環(huán)保隱患。在該試驗(yàn)項(xiàng)目建成以前,使用焚燒爐焚燒處理。近年來,針對(duì)廢堿液的處理技術(shù)工藝,一直以來都是工業(yè)廢水處理研究領(lǐng)域當(dāng)中的熱點(diǎn)之一,同時(shí)也是一大難點(diǎn)。全面針對(duì)其技術(shù)手段進(jìn)行改良和提高,是當(dāng)前煤制烯烴企業(yè)的迫切需要。
4 含堿廢水水質(zhì)
某煤制烯烴項(xiàng)目含堿廢水流量3m3/h。進(jìn)、出水指標(biāo)見表1。
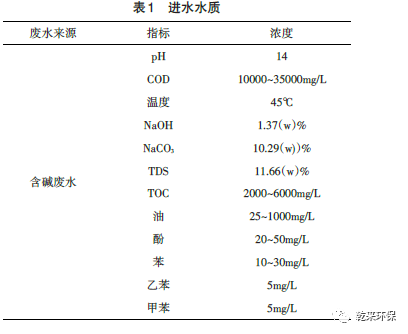
5 實(shí)驗(yàn)過程及工藝流程設(shè)計(jì)分析
現(xiàn)場(chǎng)取樣,實(shí)驗(yàn)室開始小試實(shí)驗(yàn),水樣表觀:水溫約40℃左右,水樣呈橙黃色,不透明無沉淀物,取樣瓶頂部瓶壁粘有油狀物質(zhì)。
對(duì)水樣進(jìn)行分析:水中含有油、堿、溶解性有機(jī)物,考慮水中油在運(yùn)行過程中會(huì)黏住管道內(nèi)壁、堵塞布水器、裹覆催化劑等危害,所以第一步就需要將水中的油去除。
在水中大量鹽堿存在的情況下,去除COD難度較大,原因在于:處理過程中,部分步驟需要在弱酸性條件下進(jìn)行,而在未處理水中堿分情況下調(diào)節(jié)pH值所需酸量較大,導(dǎo)致始終鹽分過高。過高的鹽分會(huì)使催化劑失活。所以,實(shí)驗(yàn)路線設(shè)計(jì)為:先除油,再除鹽堿,最后去除COD。
5.1 除油工藝的選擇:水中油包含:浮油、分散油、乳化油。實(shí)驗(yàn)室首先采用排除法對(duì)各種破乳方式進(jìn)行了一定程度的篩選,經(jīng)由多種篩選嘗試后,結(jié)果表明,采用投加破乳劑的方式為最佳除油手段。在此基礎(chǔ)上,實(shí)驗(yàn)室對(duì)各種破乳劑進(jìn)行了二次定性排除,從而選出5種破乳劑,其定量分析(即除油效果)見表2。
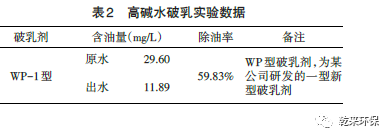
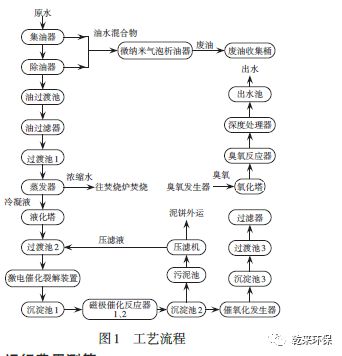
結(jié)論:由數(shù)據(jù)可知,五種破乳劑中WP-3及WP-4型破乳效果較好,結(jié)合破乳劑成本考慮,最終選擇WP-4型破乳劑為最優(yōu)選擇。WP-4型破乳劑用于廢水后,其包裹油滴形成的絮凝物難以迅速下沉,建議選擇配套氣浮類去油裝置。
5.2 除鹽堿工藝的選擇:常用廢水除鹽手段有:蒸發(fā)器、樹脂、反滲透、電滲析。其中樹脂、反滲透及電滲析對(duì)進(jìn)水要求較高,一般用在廢水的深度處理上,本工藝流程中難以實(shí)際采用,故本工藝最終選擇蒸發(fā)器為最佳除鹽堿工序。蒸發(fā)器主要有三效蒸發(fā)器和MVR蒸發(fā)器,結(jié)合運(yùn)行成本的考慮,最終選擇MVR蒸發(fā)器。實(shí)驗(yàn)室則以蒸餾工藝模擬蒸發(fā)器出水。
5.3 除COD 工藝的選擇:含堿廢水中主要有機(jī)物組成為甲醇、C6以下烴類、乙醇、二甲醚、二甲基甲酮、甲基乙基酮等,另外,還含有一定量的酚、苯等,水質(zhì)較復(fù)雜,雖然該廢水經(jīng)過了除油及蒸發(fā)工藝,但是水中殘余的有機(jī)物仍然難以用傳統(tǒng)氧化工藝或者生化工藝直接降解。
實(shí)驗(yàn)室首先采用排除法對(duì)各種物化工藝進(jìn)行一定程度的篩選,將激電催化裂解裝置、磁極催化反應(yīng)器、雙極電極反應(yīng)器、催氧化發(fā)生器、UV+臭氧曝氣、高級(jí)氧化塔等工藝分別單獨(dú)、串聯(lián)組合、改變組合順序等嘗試方法,最終選定了“高級(jí)氧化塔+激電催化裂解裝置+磁極催化反應(yīng)裝置+催氧化發(fā)生器+高級(jí)氧化塔”的五級(jí)物化工藝串聯(lián)的路線。
6 處理工藝特點(diǎn)、工藝流程設(shè)計(jì)及運(yùn)行費(fèi)用測(cè)算
6.1 系統(tǒng)介紹
6.1.1 除油:除油分三部分:(1)首先采用破乳劑使水中的分散油和乳化油脫穩(wěn)從水中析出,成為“自由”態(tài)油。(2)再經(jīng)集油器、除油器將以上所有油類與廢水分離。(3)廢油與水分離所得的廢油渣內(nèi)還有少量水分,再次將油水分離。(4)收集后油類幾乎不含水分,廢油量大幅度減少,便于廢油的下一步處理處置。
6.1.2 蒸發(fā)分離鹽、堿:除油后的廢水進(jìn)入MVR蒸發(fā)器,鹽分、堿分和部分有機(jī)物殘留在濃縮液中。部分有機(jī)物隨水蒸氣蒸離出來,形成有機(jī)物濃度較高的冷凝液,去下一處理系統(tǒng);濃縮液進(jìn)入焚燒系統(tǒng)進(jìn)行焚燒處理。
6.1.3 去除COD、提高可生化性:含高濃度有機(jī)物的蒸發(fā)冷凝液進(jìn)入氧化塔1級(jí),再經(jīng)激電催化裂解裝置,使難分解的大分子有機(jī)物開環(huán)斷鏈,轉(zhuǎn)化為小分子化合物。再利用磁極催化反應(yīng)器,在外界物理因素不變的條件下利用強(qiáng)電場(chǎng)及磁場(chǎng)輔助作用將水中的穩(wěn)定大分子官能團(tuán)破壞。然后再采用催氧化發(fā)生器,將有機(jī)物無選擇的礦化,去除水中的有機(jī)污染物。再進(jìn)入氧化塔2級(jí)及臭氧反應(yīng)器,最后再加設(shè)深度處理器保障出水水質(zhì),使其最終能滿足出水要求。
6.2 工藝技術(shù)特點(diǎn)
6.2.1 除油率高、除油徹底、廢油不含水分:本工藝對(duì)油的處理分三部分:(1)本工藝采用破乳劑將分散油和乳化油從水中分離形成浮油。(2)經(jīng)集除油器將以上所有油類進(jìn)行分離、收集。(3)廢油從設(shè)備內(nèi)脫出后,不含水分。
6.2.2 改變有機(jī)物結(jié)構(gòu)的物化預(yù)處理工藝:處理后的冷凝液要求滿足污水處理站的處理要求,污水處理站采用生化處理工藝,因此,對(duì)冷凝液的處理,不宜采用生化的工藝,否則經(jīng)生化預(yù)處理的廢水再進(jìn)入后續(xù)的生化工藝會(huì)帶來一系列的技術(shù)困難。設(shè)計(jì)側(cè)重于在對(duì)廢水中有機(jī)物進(jìn)行開環(huán)斷鏈改變有機(jī)物分子結(jié)構(gòu)的基礎(chǔ)上,降解有機(jī)物,提高BOD/COD。針對(duì)蒸發(fā)冷凝液廢水中有機(jī)物的特點(diǎn),連續(xù)運(yùn)用了氧化塔1級(jí)、激電催化裂解裝置、磁極催化裝置、催氧化發(fā)生器、氧化塔2級(jí)、臭氧反應(yīng)器及終端水處理器等工藝,通過預(yù)處理降低廢水中對(duì)生化有抑制作用的物質(zhì)含量,把分子結(jié)構(gòu)穩(wěn)定的有毒有害物質(zhì),難生化降解的大分子有機(jī)物分解成小分子有機(jī)物,提高后續(xù)工藝的可生化性。
6.2.3 新型的MVR 蒸發(fā)技術(shù)的運(yùn)用:(1)針對(duì)本項(xiàng)目廢水中含堿量較高的特點(diǎn),如采用通常的蒸發(fā)器,在堿性、溫度、拉伸力的聯(lián)合作用下,設(shè)備將不可避免地發(fā)生堿脆。因此,選擇可行的蒸發(fā)工藝成為整個(gè)系統(tǒng)的重要環(huán)節(jié)之一。MVR技術(shù)是重新利用它自身產(chǎn)生來自二次蒸汽的能量,從蒸發(fā)器出來的二次蒸汽,經(jīng)壓縮機(jī)壓縮,壓力溫度升高,熱焓增加,然后送到蒸發(fā)器的加熱層,當(dāng)作加熱蒸汽使用,使廢水維持沸騰狀態(tài),而加熱蒸汽本身則冷凝成水,這樣原先廢棄的蒸汽就得到了充分利用,回收了潛熱,又提高了熱效率。(2)針對(duì)MVR蒸發(fā)器與三效蒸發(fā)器的經(jīng)濟(jì)效能,通過測(cè)算對(duì)比得,MVR蒸發(fā)工藝要比三效蒸發(fā)工藝每年運(yùn)行費(fèi)用節(jié)約8.56萬元。
6.3 技術(shù)工藝流程,見圖1
6.4 運(yùn)行費(fèi)用測(cè)算:本項(xiàng)目運(yùn)行費(fèi)用主要包括藥劑費(fèi)、設(shè)備費(fèi)、電費(fèi)及蒸汽費(fèi)等。實(shí)際運(yùn)行噸水處理費(fèi)用為43.13元/t。
7 結(jié)束語(yǔ)
針對(duì)含堿廢水特點(diǎn),采用了實(shí)驗(yàn)室處理為試驗(yàn)基礎(chǔ),在試驗(yàn)取得成果的基礎(chǔ)上,開展工藝設(shè)計(jì),綜合利用除油設(shè)備、高效蒸發(fā)設(shè)備、COD物化處理系統(tǒng)等工藝,在某煤制烯烴項(xiàng)目現(xiàn)場(chǎng)建設(shè)一套3m3/h處理能力的中試裝置,中試裝置建好投料后,很好地去除了廢水中的油類、鹽、堿及COD,提高了廢水的可生化性,滿足了后續(xù)生化工藝的進(jìn)水要求。
7.1 試驗(yàn)結(jié)果:中試裝置正常運(yùn)行后進(jìn)行了工藝測(cè)定工作,測(cè)定工作反映系統(tǒng)運(yùn)行的真實(shí)情況,經(jīng)過連續(xù)72h的測(cè)定并送水樣檢測(cè),結(jié)果表明工藝系統(tǒng)運(yùn)行穩(wěn)定,見表3。
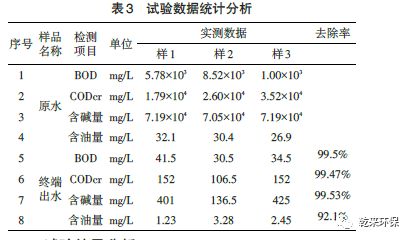
7.2 試驗(yàn)結(jié)果分析:根據(jù)中試運(yùn)行結(jié)果可知,72h 連續(xù)運(yùn)行測(cè)定的COD值分別為152mg/L、106.5mg/L、152mg/L,遠(yuǎn)小于設(shè)計(jì)值600mg/L。處理程度較深,水中大部分有機(jī)物都得到了降解,工藝處理能力大大超過設(shè)計(jì)要求,中試裝置試驗(yàn)結(jié)果也驗(yàn)證了本含堿廢水處理工藝的成功。處理后與處理前水樣對(duì)比見圖2(左:出水、中:濃縮液、右:原水)。
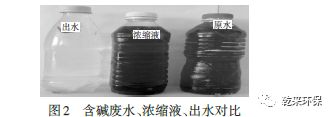
7.3 試驗(yàn)結(jié)論:本試驗(yàn)裝置的成功實(shí)踐,研發(fā)出了一套適合處理高濃度含堿水的工藝,彌補(bǔ)了國(guó)內(nèi)對(duì)此類及同類型廢水處理方法及工藝方面存在的不足,可以作為制定同行業(yè)及同類型的污水處理的標(biāo)準(zhǔn)。本工藝無論從投資還是處理效果都達(dá)到預(yù)期值,且費(fèi)用較低,該工藝較為成功地處理煤制烯烴項(xiàng)目所產(chǎn)生的高濃度含堿廢水,可進(jìn)行大面積推廣應(yīng)用。
來源:《神華科技》 作者:孫高攀
特此聲明:
1. 本網(wǎng)轉(zhuǎn)載并注明自其他來源的作品,目的在于傳遞更多信息,并不代表本網(wǎng)贊同其觀點(diǎn)。
2. 請(qǐng)文章來源方確保投稿文章內(nèi)容及其附屬圖片無版權(quán)爭(zhēng)議問題,如發(fā)生涉及內(nèi)容、版權(quán)等問題,文章來源方自負(fù)相關(guān)法律責(zé)任。
3. 如涉及作品內(nèi)容、版權(quán)等問題,請(qǐng)?jiān)谧髌钒l(fā)表之日內(nèi)起一周內(nèi)與本網(wǎng)聯(lián)系,否則視為放棄相關(guān)權(quán)益。